Dank OEE-Analyse Reibungsverlusten auf die Spur kommen
Die "Overall Equipment Effectiveness" oder Gesamtanlageneffektivität ist eine betriebswirtschaftliche Kennzahl für fertigende Unternehmen. Sie bemisst Produktivität und etwaige – ungeplante – Verluste durch Anlagen und Maschinen. Die OEE ist definiert als Produkt aus Verfügbarkeitsfaktor, Leistungsgrad und Qualitätsrate. Ihre Analyse gibt Aufschluss über die wichtigsten und häufigsten Störungen in der Fertigung: Ausfälle, Stillstandszeiten, Ausschuss, Verlangsamung et cetera.
Insbesondere für Produktionsunternehmen mit hoher Anlagenintensität wie der Automobilindustrie, dem Maschinenbau, der chemisch-pharmazeutischen Industrie, der Ernährungs- und Konsumgüterindustrie ist die Erhebung der Gesamtanlageneffektivität existenziell. Das gilt für große Konzerne ebenso wie für kleine und mittlere Unternehmen (KMU).
Die Definition der Kennzahl ist allerdings nirgendwo vorgegeben, jedes Unternehmen legt sie für sich selbst fest. Voraussetzung hierfür sind ein entsprechendes Bewusstsein für vermeidbare Verluste und Werkzeuge zur Erfassung der benötigten Daten. Viele Unternehmen setzen dazu spezielle Hard- und Software zur OEE-Analyse ein.
Zum Thema
Herkömmliche OEE-Tools benötigen größere IT-Ressourcen
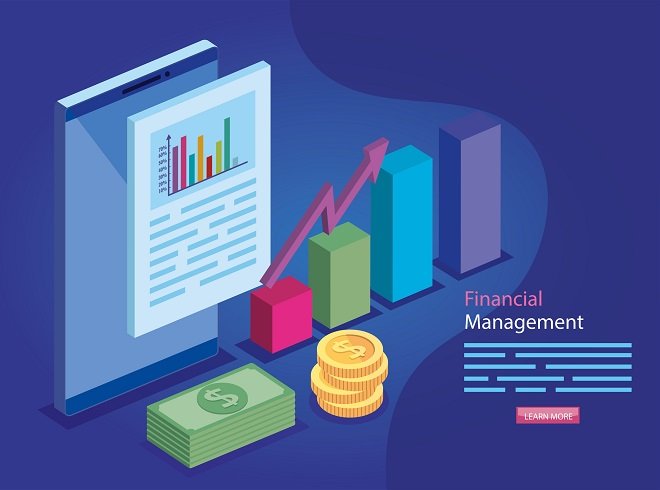
Einer der Vorzüge digitaler OEE-Analyse ist Schnelligkeit. Wenn Unternehmen entsprechende Tools einführen, wird oft innerhalb von zwei Wochen bereits eine Produktivitätsverbesserung von zehn Prozent erreicht, die sich bis zu 30 Prozent steigern lässt. Selbst eine Verdopplung der Gesamtanlageneffektivität ist keine Seltenheit.
Der zweite Vorteil ist, dass Mängel zügig diagnostiziert werden. Ausschuss verursacht dieselben Herstellungskosten wie reguläre Produkte. Nacharbeit an fehlerhaften Produkten ist aufwendig. Beides schmälert den Gewinn. Dank lückenloser Rückverfolgbarkeit lassen sich Qualitätsdefizite durch automatisierte OEE-Erfassung sofort erkennen und abstellen.
Der einzige Nachteil digitalisierter OEE-Lösungen ist, dass sie herkömmlicherweise als On-Premises- oder Cloud-Version angeboten werden, entweder also hauseigene Server und qualifiziertes Personal voraussetzen oder größere finanzielle Mittel für die eingekaufte IT-Leistung.
Für KMU in der produzierenden Industrie stellt beides eine Schwierigkeit dar. Häufig fehlen in Betrieben dieser Größenordnung die erforderlichen Ressourcen.
Dezentrale Lösungen senken die Einstiegshürden der Digitalisierung
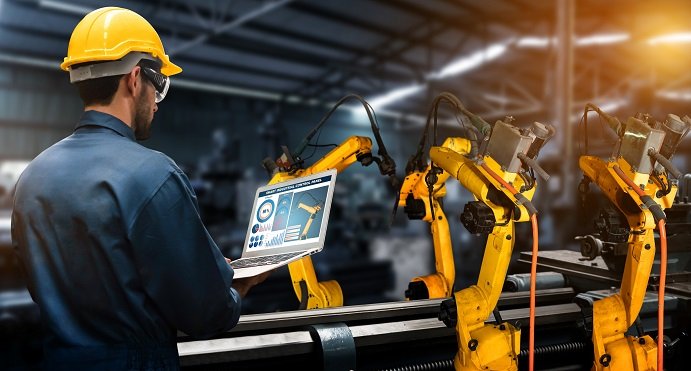
An dieser Stelle tritt die datavi GmbH aus dem oberfränkischen Rödental auf den Plan. Das junge, innovative Unternehmen hat es sich zur Aufgabe gemacht, auch kleinen und mittleren Unternehmen Zugang zu digitaler Technologie zu ermöglichen. datavi verzichtet dabei auf Cloud- sowie On-Premise-Lösungen und setzt auf dezentrale Industrial-Internet-of-Things-Technologie (IIoT), auch bekannt als Industrie 4.0. Sie ist schnell integrierbar in bestehende Produktionsprozesse, wächst mit dem Unternehmen, ist flexibel, setzt keine aufwendige IT-Infrastruktur und kein spezielles Know-how voraus und ist kostengünstig.
Für die OEE-Erfassung und -Analyse entwickelte datavi sein All Productions Control (APC). Es protokolliert alle einschlägigen Kennzahlen in Hinsicht auf Verfügbarkeit, Leistung und Qualität in Echtzeit, also Prozess- und Maschinendaten, Statusmeldungen, Verschleißzahlen et cetera.
Zusätzlich erfasst APC alle Störungen und Fehlermeldungen. Anhand dieser Daten lassen sich temporäre Soll-Ist-Abweichungen und generelle Verbesserungsmöglichkeiten erkennen. Mitarbeiter können die Anlageneffektivität kontinuierlich überwachen und bei Unregelmäßigkeiten zügig Gegenmaßnahmen einleiten. Ingenieure können Prozesse optimieren und sofort Erfolgskontrollen durchführen. Das Management kann personelle und finanzielle Ressourcen vorausschauend steuern.
Für den Einsatz von All Productions Control ist keine spezielle IT-Struktur notwendig. Benötigt wird lediglich ein Ethernet-Anschluss an der Maschinensteuerung. Er ist normalerweise als Standardschnittstelle bereits vorhanden oder kann problemlos nachgerüstet werden.
Ergänzende Hard- oder Software und Programmierkenntnisse sind ebenfalls nicht nötig: Das Tool beinhaltet alle Funktionen zur Aufnahme, Speicherung und Bereitstellung der Daten, visualisiert sie übersichtlich im Dashboard und archiviert sie.
Dank fachlicher Expertise und herausragender Kundenorientierung konnte datavi bereits etliche Unternehmen erfolgreich darin unterstützen, den höchstmöglichen Nutzungsgrad ihrer Maschinen und Anlagen auszuschöpfen.
Motiviert von dieser Erfahrung erarbeitet das Team aktuell ein Werkzeug zur Digitalisierung der gesamten Fertigung. Das "Digitale Schichtbuch – MES" wird zukünftig die Schicht-, Produktions- und Prozessplanung erheblich vereinfachen.
Wer sich von den zahlreichen Vorteilen von APC "im laufenden Betrieb" überzeugen möchte, kann das Tool in einem ersten Pilotprojekt ausgiebig testen.
- Herr Patrick Dabrowski
- Coburger Straße 7
- Gebäude 2
- 96472 Rödental
- Deutschland