Industrie 4.0: Optimierung statt Stillstand!
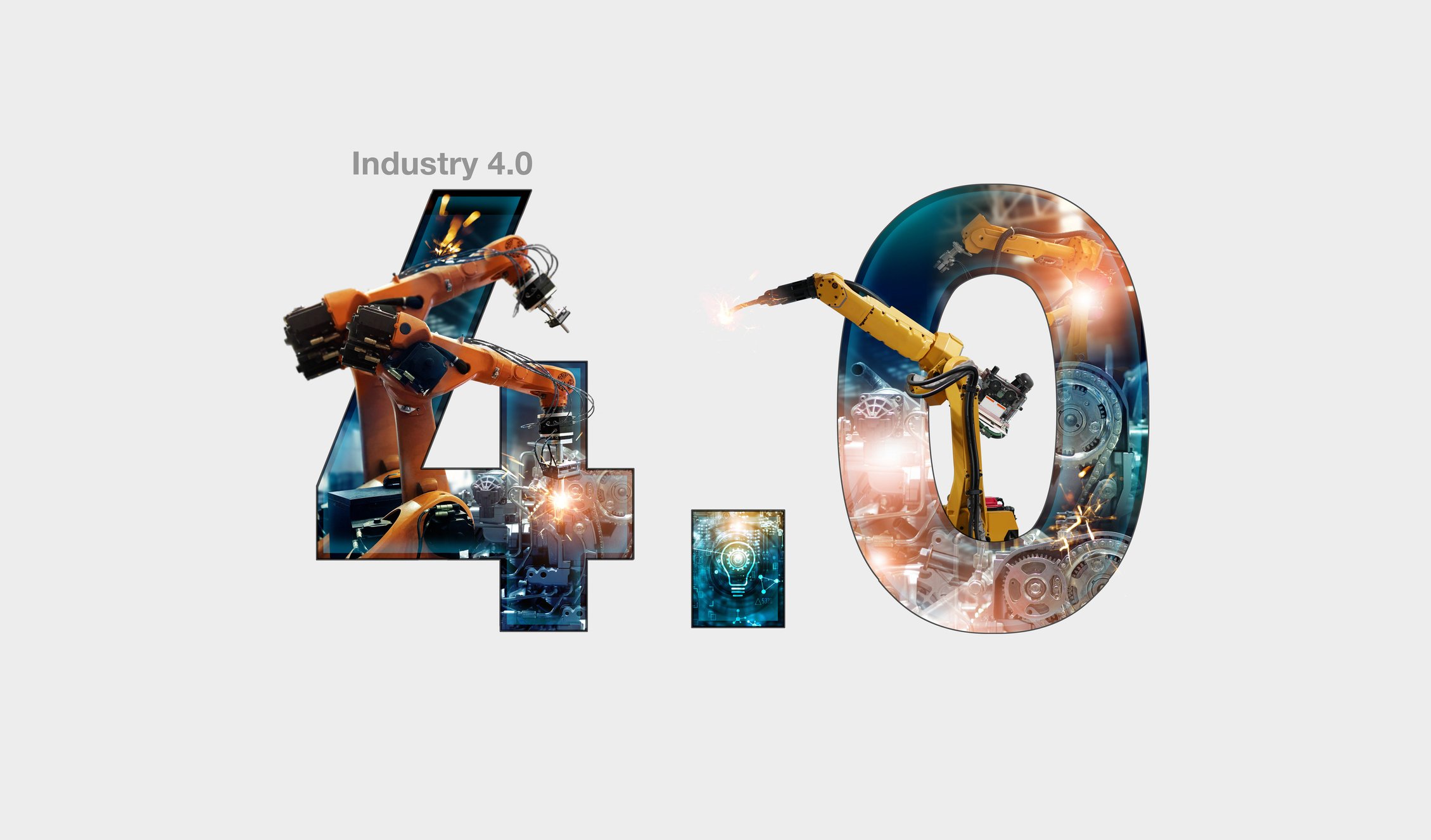
Um in der Fertigung eine größtmögliche Produktivität zu erreichen, ist Transparenz das Schlagwort der Stunde. Denn nur durch ein umfassendes Wissen über alle Prozessvorgänge können diese optimiert und an wechselnden Gegebenheiten angepasst werden. Schließlich befindet sich ein (wachsendes) Unternehmen immer in gewissen Umbrüchen, sodass Veränderungen und Optimierungen zum Produktionsalltag gehören sollten.
Die hierfür so zwingend benötigte Transparenz muss Zahlen, Daten und Fakten offenlegen – idealerweise mittels OEE-Kennzahl. OEE ist die Abkürzung für "Overall Equipment Effectiveness". Dies bedeutet übersetzt so viel wie "Gesamtanlageneffektivität" und bewertet Produktivität einer Anlage oder Maschine. Die Produktionskennzahl OEE wird aus dem Produkt von Verfügbarkeits-, Leistungs- und Qualitätsgrad berechnet und schließt auch die Verluste durch ungeplante Stillstände, Abweichungen von der angestrebten Stückzahl sowie durch nicht brauchbare Teile ein.
Somit liefert eine OEE-Analyse exakte Zahlen zur Orientierung über die Produktivität eines Unternehmens und bietet die Basis für eine OEE-Optimierung. Hierbei werden Maschinen und Anlagen nicht nur in Echtzeit während der gesamten Produktionslinie überwacht und Fehler oder Störungen im Produktionsablauf angezeigt sowie Schwachstellen im System deutlich gemacht. Auch lassen sich Erfolge und Misserfolge von durchgeführten Maßnahmen erkennen und auswerten, sodass eine ständige Optimierung möglich wird.
Zum Thema
Digitalisierung in der Fertigungsbranche: Die Vorteile einer OEE-Optimierung richtig nutzen
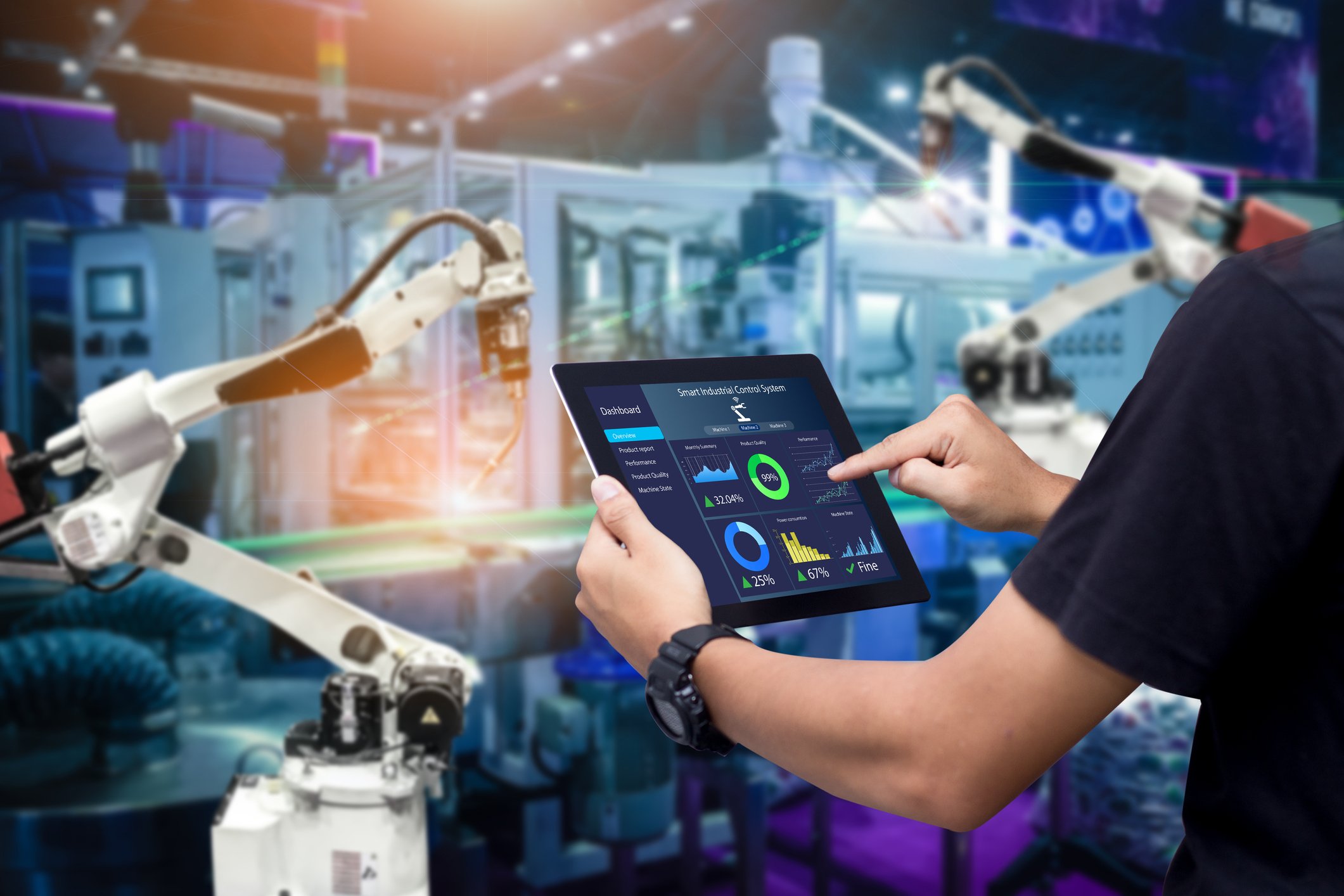
Die Vorteile einer digitalen OEE-Erfassung und OEE-Optimierung sind, im Gegensatz zur manuellen, besonders signifikant. Möglich wird die digitale Erfassung durch ein APC, ein "All Productions Control", wie das vom jungen Digitalisierungsspezialisten datavi. Das APC von datavi sorgt für maximale Transparenz während der gesamten Produktion und gilt als Herzstück aller Prozessabläufe. Dabei protokolliert das APC wichtige Kennzahlen hinsichtlich Verfügbarkeit, Performance und Qualität von Produktion in Echtzeit und visualisiert diese. So ist immer genau ersichtlich, was wo passiert, wo Probleme auftreten und wann die Produktionskette neu justiert werden muss, um profitabler zu sein. Dank dieses APC lässt sich also ganz leicht das Maximum aus einer Maschine herausholen.
Die Einbindung des APC von datavi in die unternehmenseigenen Systeme ist schnell und einfach, schon nach kürzester Zeit ist alles einsatzbereit. Die Darstellung der erfassten Daten geschieht in unterschiedlichsten Ausführungen und ist dabei stets übersichtlich – sodass eventuelle Probleme an Maschinen oder Anlagen umgehend erkannt werden und ein Eingreifen sofort möglich ist. Durch die automatische Datenerfassung sind die Messungen äußerst genau und die Fehlerquote wird deutlich gesenkt. Im Gegensatz zu einer manuellen Messung, die häufig mit Toleranzen zu kämpfen hat, die sich summieren und schließlich zu größeren Unstimmigkeiten führen können.
Anders als bei der manuellen OEE-Erfassung erfolgt die digitale kontinuierlich und stets nach demselben Muster. Dadurch sind die erhobenen Daten zu jeder Zeit reliabel. Und weil bei der digitalen OEE-Erfassung keine Mitarbeitenden benötigt werden, kann deren Arbeitskraft anderweitig eingesetzt werden. Somit ist die automatische Datenerfassung nicht nur weniger fehleranfällig und wesentlich genauer, sondern sie erlaubt zudem eine wesentlich höhere Produktivität.
OEE-Optimierung: Warum die Lösung von datavi auch hinsichtlich Nachhaltigkeit überzeugt
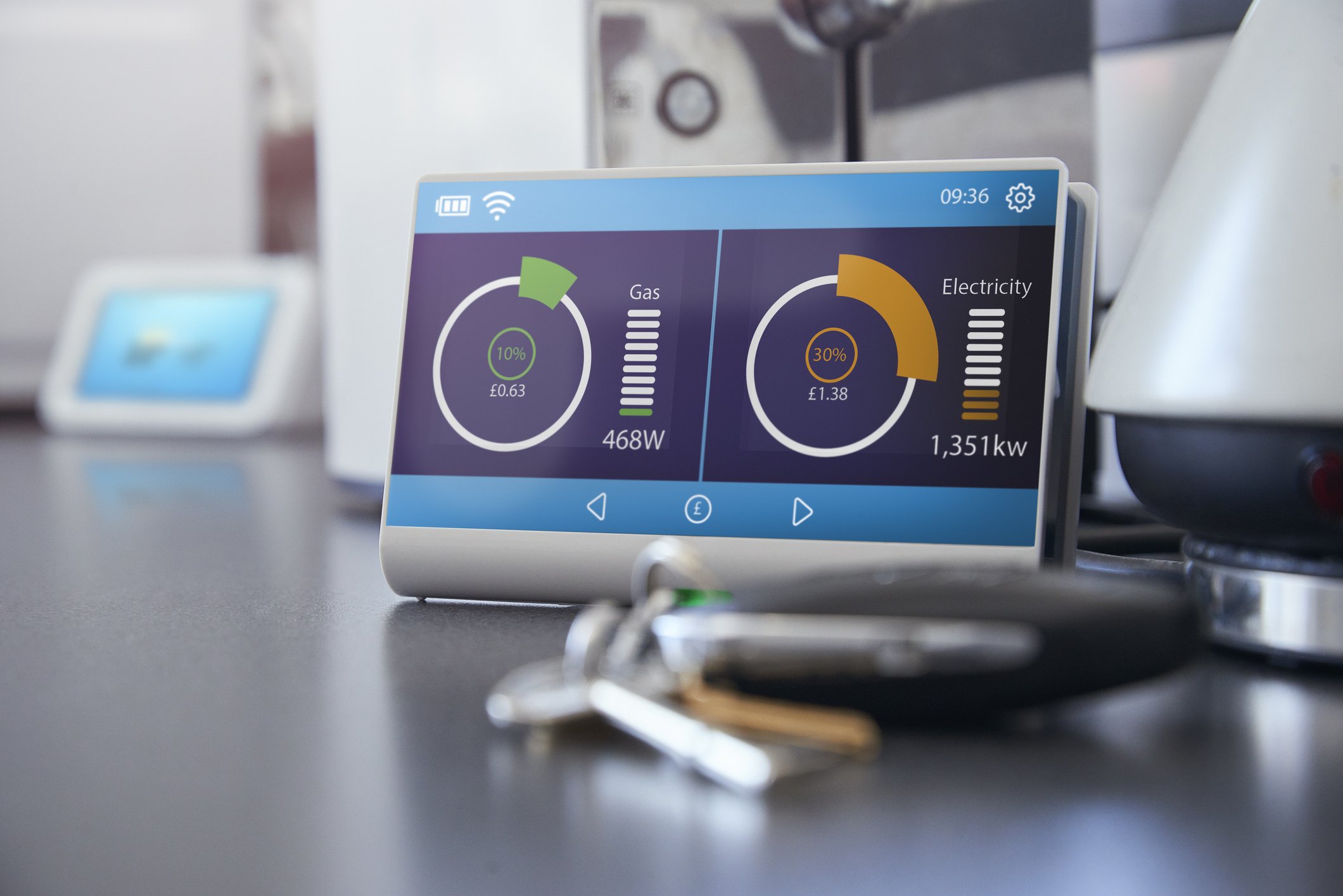
Aktuell besonders interessant ist die Visualisierung des Energiemonitorings und des OEEs, das jeweils übersichtlich auf dem Dashboard erfolgt. Aufgrund der stark gestiegenen Energiepreise, die weiten Teilen der Wirtschaft stark zu schaffen machen, können durch ein lückenloses Monitoring alle vorherrschenden Verbrauchsmuster analysiert und ausgewertet werden. So lassen sich Strom- und Druckluftverbrauch einzelner Abteilungen identifizieren, sich anbahnende Lastspitzen vermeiden und der gesamte Energieverbrauch kann einfacher in Relation zur Maschinenleistung gesetzt werden.
Ein weiterer wichtiger Baustein zur Industrie 4.0 von datavi ist das digitale Schichtbuch. Dieses ermöglicht die Führung, Lenkung, Steuerung und Kontrolle der Produktion auf Betriebsleitebene – in Echtzeit und unter Einbindung benutzerfreundlicher Software bis zum Maschinenbediener. Durch digitale Arbeitsaufträge, umfassende Datenerhebungen und Materialinformationen werden mit dem digitalen Schichtbuch eine effektive Planung und Durchführung der Fertigungsprozesse in kürzester Zeit und mit weniger Ressourcen möglich.
Die Komplettlösung von datavi überzeugt auch deswegen, weil sie ohne feste Cloud oder Serverstruktur auskommt. Stattdessen werden alle Daten auf jedem einzelnen APC gespeichert, verarbeitet und bereitgestellt, sodass keine zentrale Speichereinheit nötig ist. Diese Lösung ist nicht nur preiswerter, sie ermöglicht zudem eine Installation und eine Inbetriebnahme in der Hälfte der dafür üblichen Zeit. Der Zeitvorteil ist also enorm. Auch ist die Lösung von datavi zu 100 Prozent skalierbar und nicht abhängig von der internen IT-Infrastruktur. Es spielt also keine Rolle, ob 10 oder 100 Anlagen an das System angebunden sind.
Somit vereint datavi einen sehr detaillierten Analyseansatz großer Allroundlösungen mit flexiblen, simplen und preiswerteren Ideen kleinerer Anbieter. Zudem sind das Alter und die Art der Anlagen irrelevant, sodass der komplette Fertigungsprozess mit verschiedenen Produktionsverfahren in einer digitalen Lösung vereint werden kann.
Hinter datavi steckt ein innovatives IT-Unternehmen mit Sitz in Coburg, dessen hoch motiviertes, junges Team die Industrie 4.0 im Fokus hat. Diese soll für allen Unternehmen greifbar und real werden mit dem Ziel, eine maximale Transparenz in der gesamten Produktionsumgebung zu erreichen.
- Herr Patrick Dabrowski
- Coburger Straße 7
- Gebäude 2
- 96472 Rödental
- Deutschland